Comfort and infotainment
Adhesives and sealants for comfort and entertainment applications
For many car buyers, comfort and entertainment functions are now more important than motor performance. Huge displays and seamless connection to the owner's smartphone is just the beginning. Most experts agree that cars are set to become operating systems on wheels.
Adhesives and sealants are essential for practically all comfort and entertainment functions, from visual displays and sound systems to haptic experiences in the form of massage seats and active roll stabilization when cornering.
Display bonding in cars: From the cockpit to the control center
Navigation, infotainment, and input screens as well as head-up displays consist of different assemblies that must be permanently connected to each other. Various adhesives can be used for structurally bonding display frames to protective glass, for bonding and sealing displays in housings, for connecting functional components for haptic feedback, and for constructing head-up displays. Especially DELO PHOTOBOND UV acrylates show very much improved outgassing behavior compared to silicones and reach full strength within seconds under UV light.
Applications
- Cockpit information systems
- Cockpit instrument displays
- Car audio and infotainment displays
- Navigation and entertainment systems
- Display protection glass
- Head-up displays
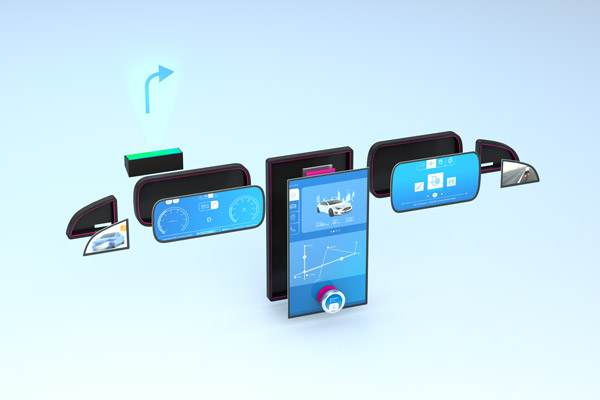
When integrating displays into assemblies, the most important thing is to create a tension-free and reliable connection between the display glass and the frame as well as between the different materials of retainers, housings, and for active components. Something else to consider is the size of the assemblies, which often requires the use of room-temperature-curing adhesives.
DELO has developed special adhesives with optimum properties that allow for fast production processes. This range includes DELO PHOTOBOND adhesives that can be preactivated with light and then cured by humidity, thus enabling “curing on demand”. Even opaque components can be bonded quickly and reliably with these products.
Typical bonding tasks
- Structural bonding of displays to frames and housings
- Sealing of housings
- Bonding of operating elements to display protection glass
- Bonding and protection of various components such as COG/COF or flex conductors to displays
- Bonding of functional components to the display structure (haptic feedback)
- Bonding of various components in head-up displays
Speaker adhesives
Many car buyers attach importance to clear trebles and deep basses. A high-performance sound system can therefore give OEMs an edge over competitors. The right adhesives are essential to ensure that speakers deliver clear tones throughout. This also applies to the many mini speakers in the car, which you hear when operating the turn signal or parking, for instance.
DELO has developed special products for speakers whose coordinated properties help enhance speaker acoustics. The adhesives fulfill the technical requirements for high power density as well as high temperature stability and resistance, while enabling fast and fully automated production.
The light-curing DELO PHOTOBOND adhesives are used to bond coils to membranes and membranes to frames, for example. They are also suitable for applications such as membrane damping, wire fixation, and contact sealing. Adhesives from the DELO MONOPOX or DELO-ML range are generally used for magnet system bonding.
DELO adhesives and the equipment necessary for adhesive processing are used by leading companies in the speaker industry.
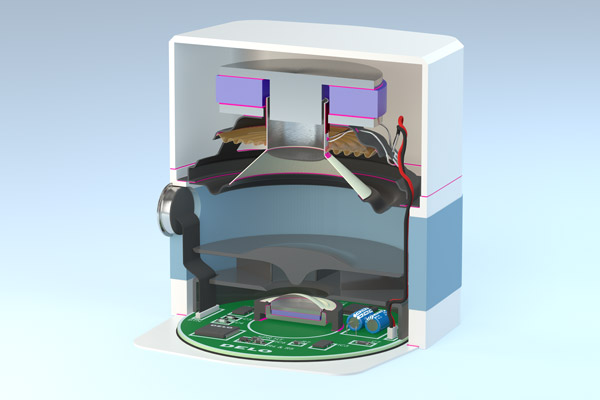
Properties
- Good adhesion to typical materials such as coated metals and ferrites, PEEK and TPE
- Very good humidity and temperature resistance
- Pass mechanical shock tests and acoustic qualification tests
- Optimized for acoustic properties
- Fast and easy dispensing by means of dispensing tip or jetting
- Very fast curing (1 s) with DELO LED curing lamps
Comfort and safety sensor materials
When it comes to sensors for comfort and safety functions such as rain and tire pressure sensors, DELO materials are used as structural adhesives, sealing compounds and protective potting compounds and encapsulants. They not only satisfy application-specific automotive requirements, but also offer maximum production efficiency. Dual-curing adhesives, with their two curing steps, are particularly suitable for this purpose. After a preceding light curing process, which allows quick prefixation for further processing, a second curing mechanism ensures reliable final curing of the adhesive even in shadowed areas. This can be triggered in various ways, for example, by heat input, by humidity, or by anaerobic effects. High volumes can therefore be achieved on production lines.
Control units for motor or on-board electronics must be protected from humidity, media and corrosion, even under extreme temperatures. The most important task for adhesives and sealants is therefore the long-term protection of the control unit housing, plugs and other microswitches in the car. Another typical application is thermal management for power electronics. In air conditioning systems, for example, thermally conductive adhesives ensure that the heat generated under load is quickly dissipated to a heat sink.
Many DELO adhesives and sealants are developed specifically for these applications and for some of their special requirements, such as bonding to certain surface coatings. They provide the necessary reliability while enabling efficient production processes thanks to full curing or fixation within seconds and the enabling of in-line tightness testing.
Sealants reliably seal plug pins for control units, for example.
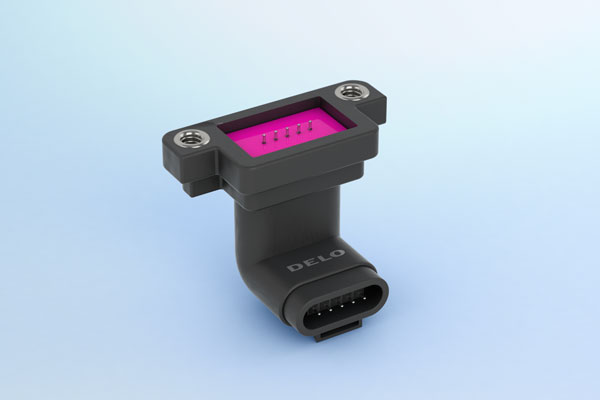
DELO products properties / strengths
- Very good sealing effect
- Good thermal cycling and media resistance
- Fast curing
- In-line tightness testing
Bonding decorative elements attractively
Decorative elements and trims such as the chrome rings on ventilation slots, real wood trim on doors and steering wheels, and cladding in the dashboard area, are bonded. Unlike screws, adhesives are invisible and more reliable than snap fits.
DELO adhesives, no matter whether in the form of "normal" liquid adhesives or as liquid pressure-sensitive adhesives – i.e. "liquid tapes" – not only fulfill mechanical and thermal requirements in the interior, they also display their special strengths in the production process. They are therefore also suitable for the most complex geometries and enable a fast light curing process for even opaque materials such as chrome rings. Thanks to what is known as preactivation, the adhesive remains liquid immediately after dispensing and a short irradiation phase so that even opaque components can be joined. After this open time, the adhesive cures within a few minutes without light influence.
The process is comparable for liquid pressure-sensitive adhesives. After irradiation, the surface is tacky. Since the adhesive reaches its initial strength immediately after the second component is pressed on, the bonded assembly can be processed directly and without temporary fixing.
DELO's interior and decorative element solutions are available both on the basis of more flexible acrylates and of stronger epoxy resins for structural applications.
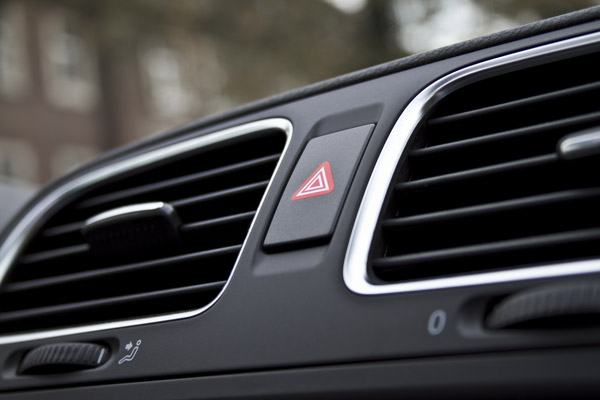
DELO products properties / strengths
- Good resistance to thermal cycling
- Good flexibility
- Fully automated production
- Also for opaque materials
- Also available as liquid pressure-sensitive adhesives
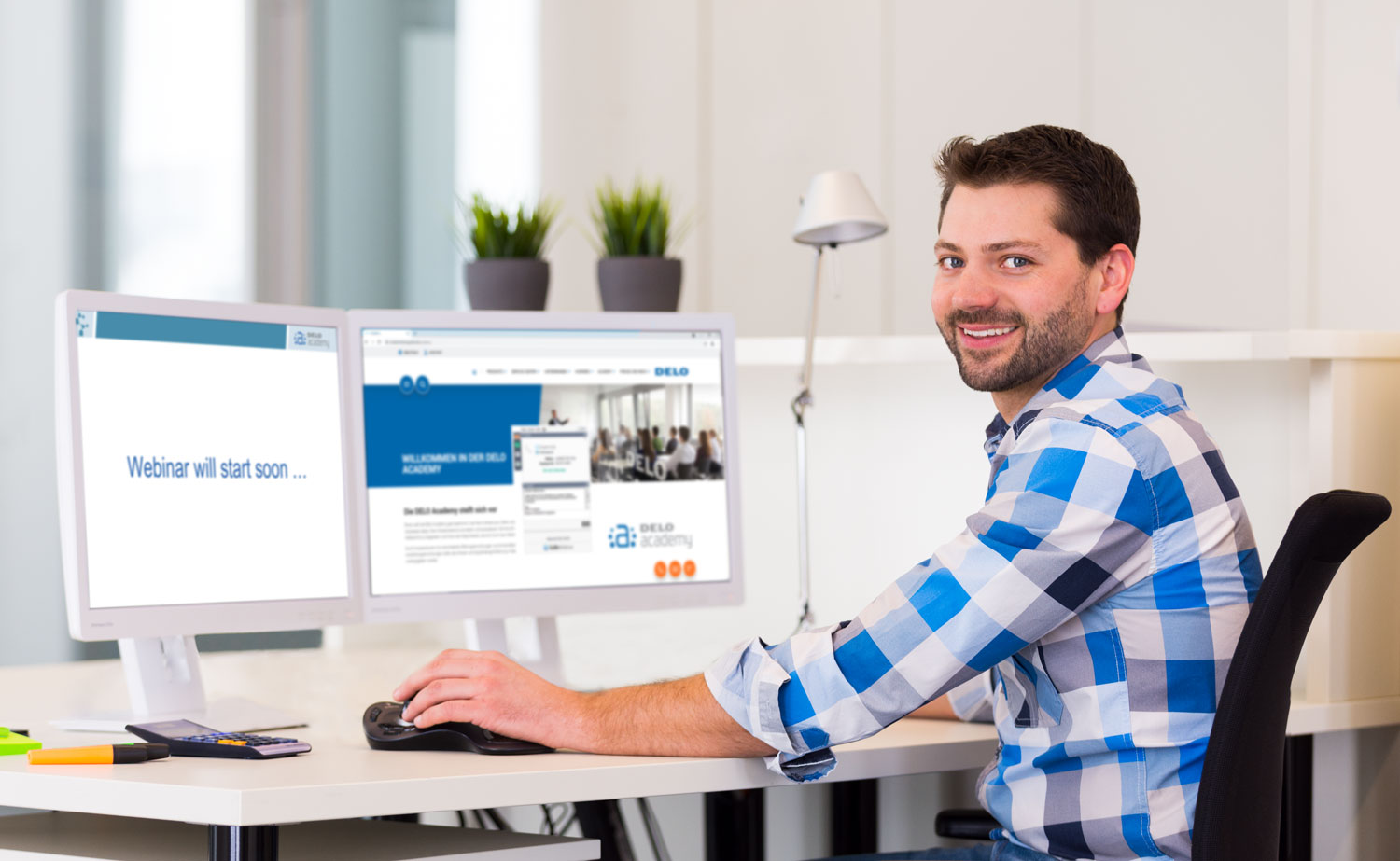
Knowledge in online format
Adhesive bonding is a demanding joining technology. To successfully solve bonding challenges, you need a good understanding of the basics and special features of this technology. Build up valuable knowledge with the help of our "TECH TALK" webinars!
Quick Request
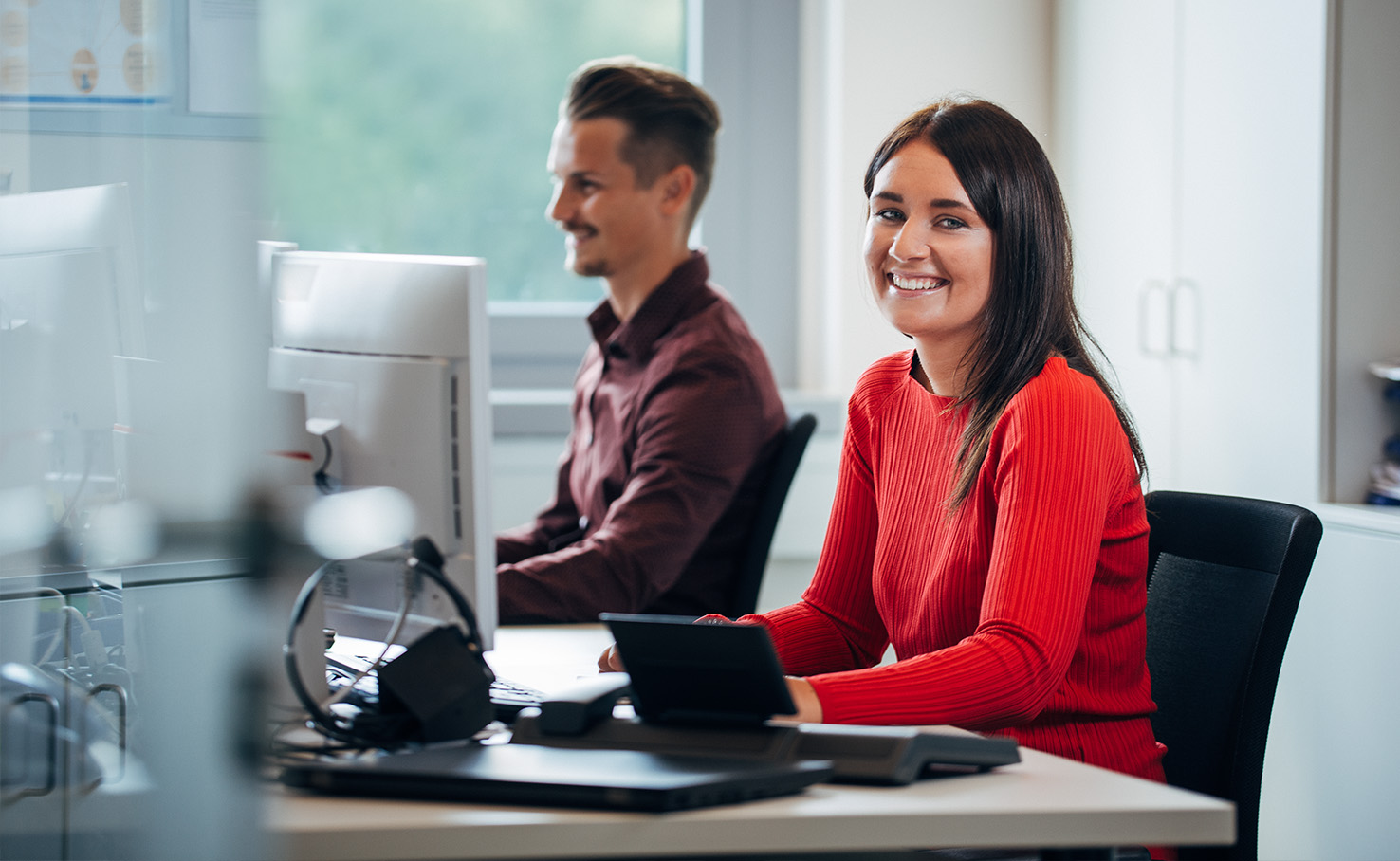