Adhesive for Semiconductor packaging
Die attach adhesives and flip-chip bonding: Safe and lasting adhesion for electric contacts
Flip-chip bonding has obvious advantages over chip-on-board (COB) technology when it comes to mounting unpackaged semiconductor chips on circuit boards: Where COB technology needs four steps, flip-chip bonding is done in two. Flip-chip contacting uses electrical connectors in the shape of 'contact bumps' on the semiconductor chip's active side. Microchips from manufacturers only need to be placed into the pre-applied adhesive – and cured. Compared to COB technology, manufacture saves two process steps: electrical contacting and chip encapsulation. DELO carries both die attach adhesive solutions and anisotropic, conductive glues. DELO is also in the lead when it comes to flip-chip processes in RFID applications!
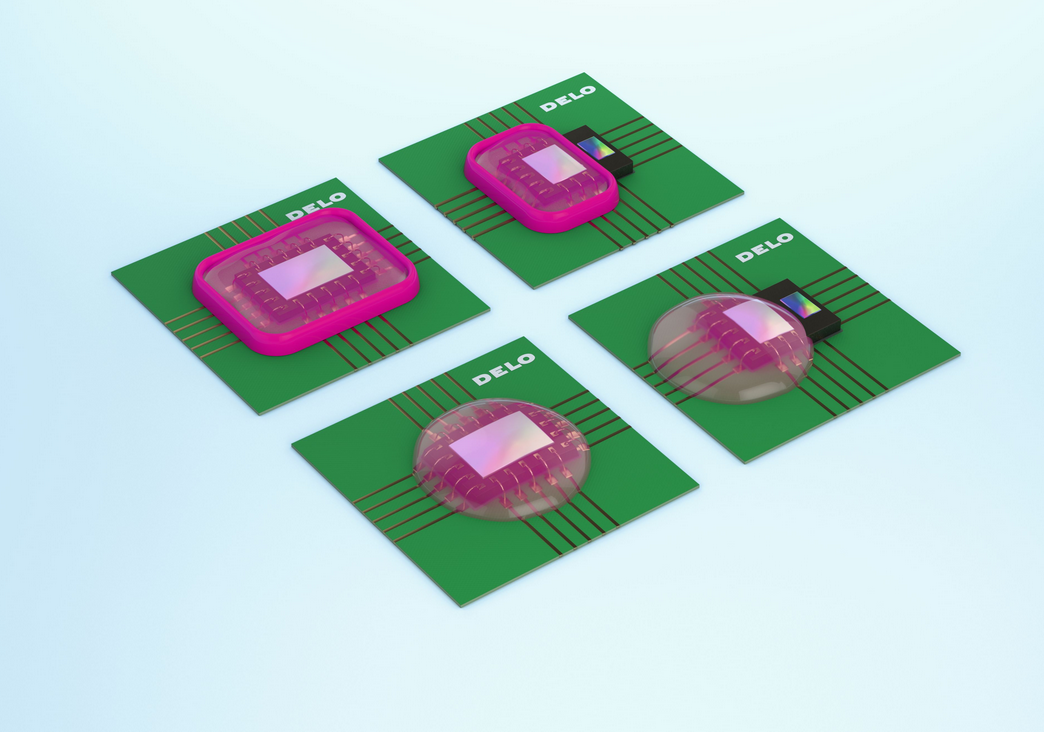
Realize miniaturization goals with DELO glue and die attach adhesive solutions
Semiconductor packaging moves towards miniaturization and thinner chips. Demands are manifold, such as superb reliability, easy processing, short cycle times and various applications in smart cards. This calls for tailored adhesives! Especially when it comes to die attach adhesive solutions, products for COB technology and flip-chip bonding, DELO offers a broad range of innovative solutions. Find out more about DELO's portfolio for semiconductor packaging online!
Properties
- Optimized products for various chip sizes
- Improved flow behavior
- Solder-free joins are possible
- High temperature stability up to +260 °C
- High ion purity, Halogen-free
- Products tested according to JEDEC MSL 1
- UV-curing and heat-curing solutions are possible
- Excellent adhesion to many substrates
Die Attach
Die attach adhesives in leadframe packages require a high temperature resistance for lead-free soldering processes, good electrical and thermal properties, and the possibility of low-tension curing. DELO has adapted its products to exactly meet these requirements.
Possibilities of use
- Semiconductor leadframe products
- Die attach with low Young’s modulus for MEMS packages
- Die attach for organic substrates
Encapsulants for the chip-on-board (COB) technology
RAFI Eltec GmbH, Überlingen, Germany, uses the DELO MONOPOX anhydrides as Dam&Fill. For the assembly, solder deposits are attached to the bottom in the form of BGA ballings, followed by one-side SMD assembly. The SMD assemblies produced are subsequently Dam&Fill-encapsulated.
In this method, two beads of adhesive are circumferentially dispensed as “Dam” on top of each other, which are subsequently “Fill”-ed. For this purpose, a screw dispensing valve is used in order to ensure that the components are evenly dispensed. Afterwards, the components are laser-marked on the encapsulation that has been cured in an air convection oven at +150 °C for 20 min.
Adhesive processing is reliable, and planar, large-area encapsulation geometries are possible. In addition, the adhesive fulfills all requirements on solder resistance. The dispensing profile can easily be adjusted to the specific package geometry, enabling high flexibility in production. It also gives a very homogeneous processing behavior, protects the component resp. the sensitive electronic parts from environmental influences, and performs excellently in reliability qualification tests. The material’s properties minimize the stress in the package. Thanks to the planar encapsulation, the component can be assembled just like a BGA module.
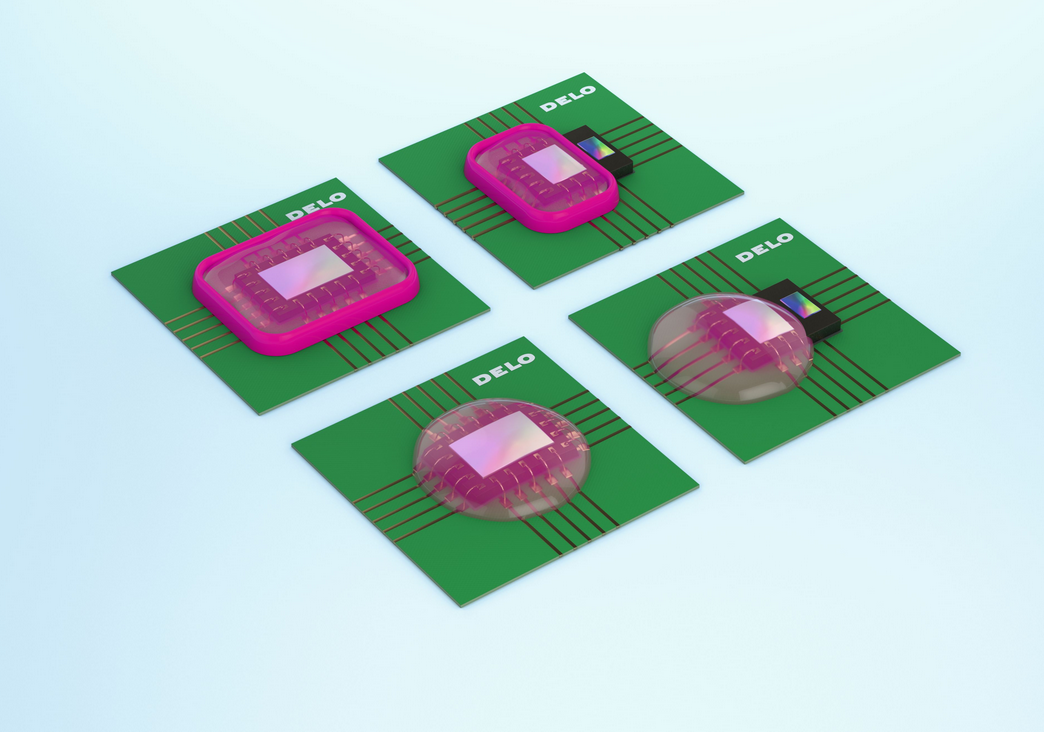
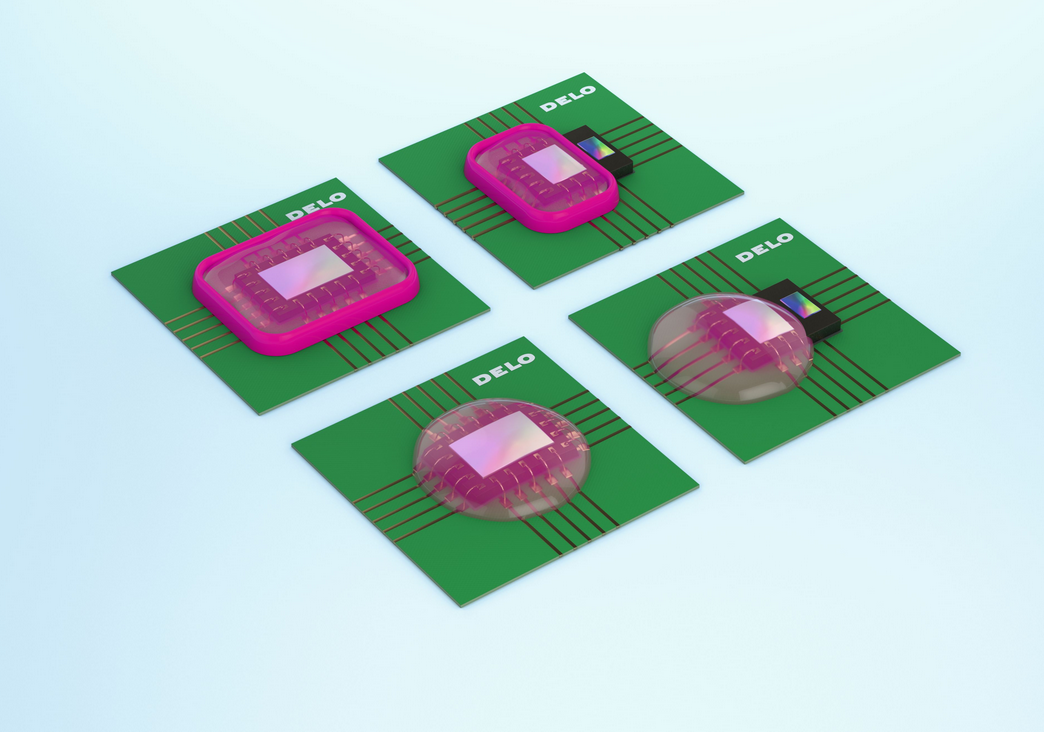
Sealing of sensors
The new anhydrides have proven successful in practice. These products are used in oil pressure sensors in cars. They cast the inside of the sensor and also seal the electrodes.
In comprehensive stress tests, the sensors casted with DELO MONOPOX proved to be completely tight. The tests included long-term storage at +150 °C, storage in ATF oil at +150 °C for 1000 h, 1000 cycles temperature shock at -40 / +150 °C, the VDA climate test, as well as customer-specific vibration tests and mechanical shock tests.