Drive train and electric mobility
Adhesives for drive trains and electric mobility
Combustion engines and electric drives are no different in one aspect: Wherever power is generated, so is heat, even in the most efficient of motors. Therefore, adhesives, sealants and encapsulants for motor-related applications must display high temperature resistance and be able to withstand the thermal influence. DELO offers an extensive portfolio of high-temperature-resistant products that also display exceptional chemical resistance. DELO adhesives are also characterized by a low coefficient of thermal expansion, which makes them ideal for use in power electronics. In the production of fuel cell stacks, the adhesives not only ensure a reliable seal, they also enable a fast and energy-efficient assembly process.
Adhesives for electric motors
Adhesives play an important part in making electric drives smaller and more powerful, while increasing their efficiency. For example, the installation space required for traditional production processes can be reduced thanks to narrow bonding gaps. Typical bonding applications for electric motors include the securing of buried or surface magnets, the stacking of segmented magnets and the bonding of stators and housings. Adhesives are also used for potting coils or for electrically insulating windings.
Suppliers benefit from DELO's extensive product portfolio. Specially developed for electric motors, the products offer maximum strength; they are temperature- and media-resistant, gap-filling, impact-resistant and tension-equalizing. Depending on the production process, curing is possible by heat, under the exclusion of air or, in the case of two-component products, at room temperature. If higher demands are placed on bonding accuracy, or if direct and fast further processing is required, such final curing is often preceded by initial light fixation. DELO therefore not only enables flexible, but also scalable and efficient production processes.
A host of bonding applications can be found in the electric motor.
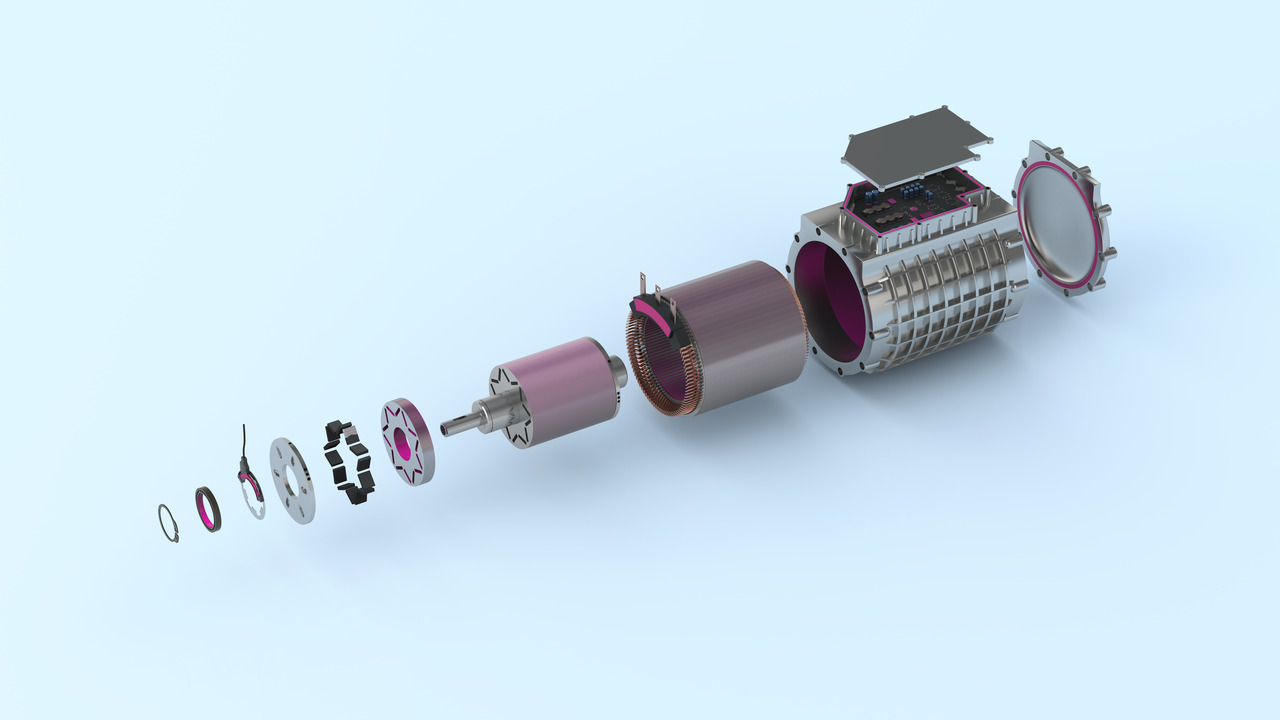
DELO products properties / strengths
- Pass automotive aging tests (e.g. 3,000 h / +180 °C)
- Maximum structural strengths
- Exceptional temperature and media resistance
- Light fixation for fast processes
Adhesives and sealants for fuel cells
On the road to CO2-neutral mobility, the use of hydrogen in the transport sector is becoming increasingly important. The required electrical energy is generated in a fuel cell from the reaction of hydrogen with oxygen, whereby only heat and pure water are produced. This makes completely emission-free driving possible if the hydrogen is produced from renewable energies.
DELO adhesives can be used for various applications within a fuel cell stack, which consists of a large number of individual fuel cells. For example, they enable the connection and sealing of the two half-shells that make up a bipolar plate. They also ensure that the media circuits (hydrogen, oxygen, coolant) of the stack are reliably sealed to each other and to the outside. Finally, our adhesives can also be used to fix components, such as the gas diffusion layer, within the stack assembly to ensure fast further processing. The light-curing or pre-activatable adhesives and sealants are always optimized for fast, precise and fully automated production, which ensures maximum production efficiency, especially in the start-up of large-scale production.
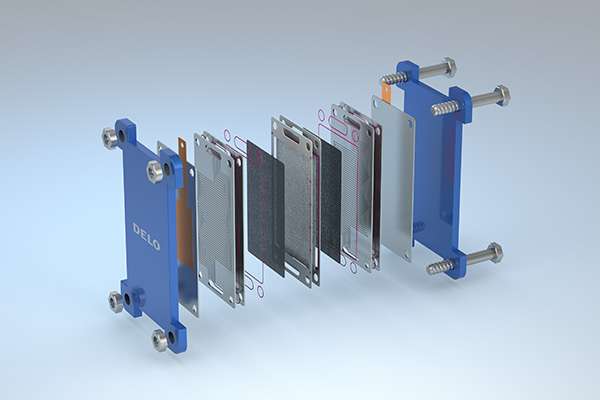
Properties / Strengths of DELO products:
- Application and curing in a few seconds
- Reliable sealing
- Energy- and resource-saving process
- Flexible design of the sealing contour
- High process reliability in assembly and operation
Adhesives for power electronics
Alongside the electric motor and energy storage system, power electronics are one of the core components of the electric drivetrain. As the link between the electrical energy sources, consumers and storage units, it controls all power flows in electric vehicles, converts DC and AC voltages into each other, adjusts voltage levels and conducts the electrical power to the electric motor.
Examples of applications for DELO adhesives in power electronics, e.g. in an inverter, range from component fixation on printed circuit boards to the thermal bonding of semiconductor elements and the encapsulation of certain components to protect them from chemical and mechanical influences. Typical requirements for the adhesive include high temperature and media resistance as well as the ability to compensate for different coefficients of thermal expansion of individual electronic components. Optimum flow behavior and fast curing with light and/or heat offer corresponding speed advantages in highly automated assembly processes.
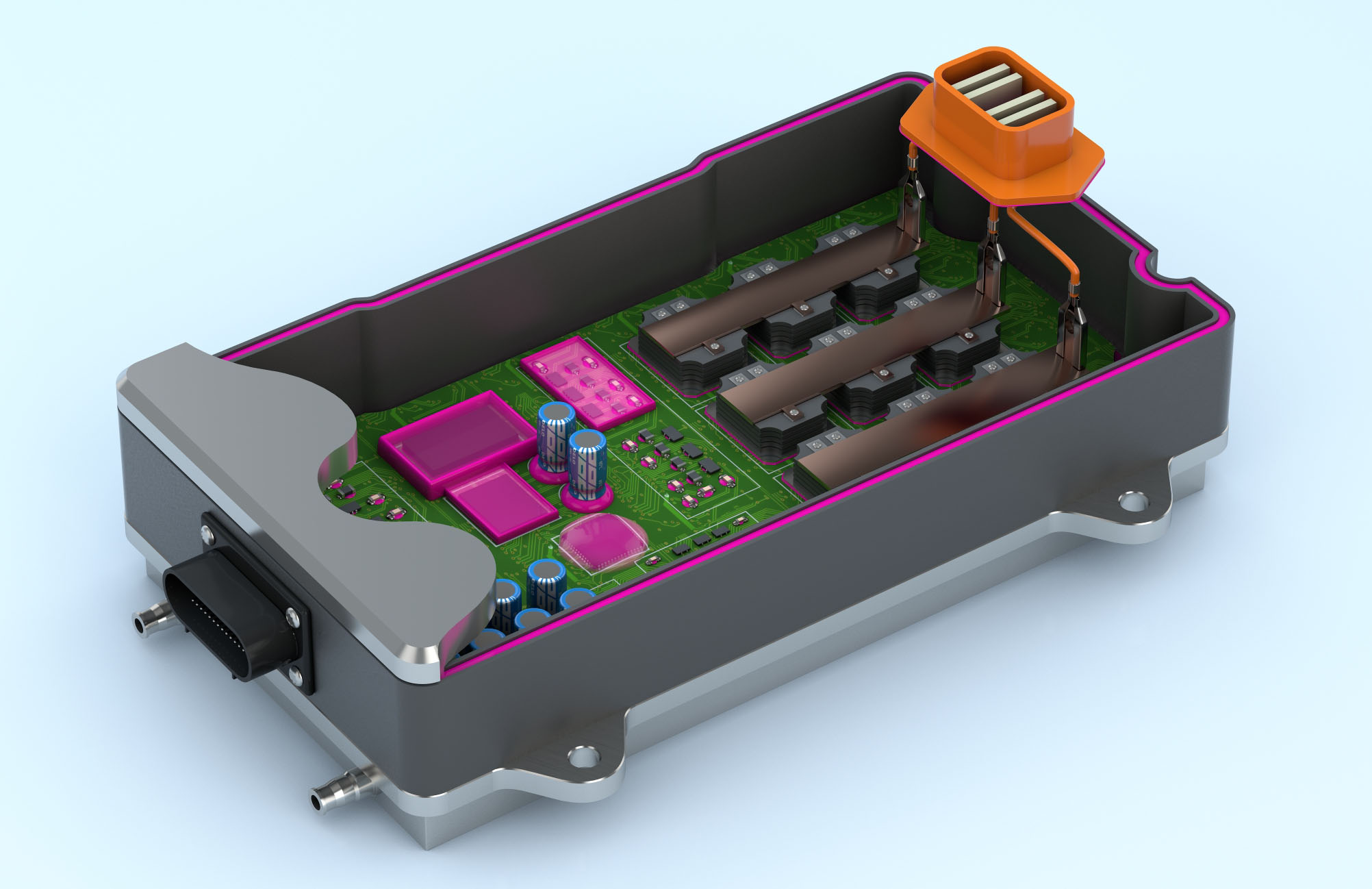
Properties / strengths of DELO products:
- Good adhesive strength on FR4 and various metals
- High temperature resistance and strength
- Low coefficient of thermal expansion
- Excellent dispensing properties
Battery adhesives
Whether purely electric cars, plug-in or mild hybrids - batteries are used in all types of electric vehicles. Depending on the design of the battery and the cell format used, the requirements for the battery adhesives used and the associated application process can be very different.
DELO adhesives are primarily used in the production of battery modules and packs. There they not only take on structural tasks. In many cases, they also dissipate the heat generated during operation and are flame-retardant. Tightness requirements, even under the influence of temperature, are often added to this. In view of the increasing numbers of electric cars of all kinds, suppliers also benefit from DELO's expertise with fast production processes. In addition to classic heat curing or room temperature curing, light curing and light fixing offer many options for efficiently producing higher volumes, particularly in the case of carrier bonding, i.e. the bonding of cylindrical cells into a carrier element.
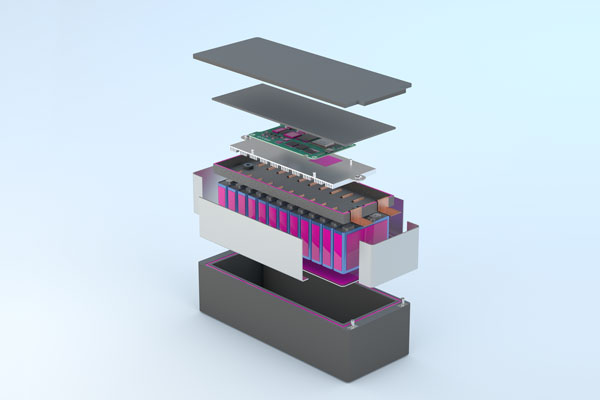
For further information take a look in our White paper:
Thermally conductive adhesives for low voltage battery cells
DELO products properties / strengths
- High structural strengths
- Reliable sealing
- Excellent aging resistance
- Good thermal conductivity
- Flame protection: UL 94 V-0
Encapsulants for sensors for the engine compartment
Sensors in the motor compartment make the highest demands of adhesives and encapsulants. Rotor position sensors and (T)MAP sensors are good examples. MAP sensors measure intake air temperature and pressure. In order to protect them, highly reliable epoxy resins, 1C and 2C products are used for the sealing of pins and potting of printed circuit boards.
The potting must remain tight at pressure differences of up to 20 bar. Appropriate products must also be resistant to oil, gasoline, and brake fluid, and be suitable for use in a service temperature range from –40 °C to +160 °C. The potting on the sensor must not display any stress cracks and no interaction between media and potting compound must take place even after constant storage or several abrupt thermal cycles. An adjusted coefficient of thermal expansion (CTE) is required to equalize tensions between the FR4 PCB material and the plastic housings.
DELO products satisfy these requirements and also display good flowability. This ensures that the encapsulant can be quickly and evenly dispensed into the housing under vacuum, also filling narrower gaps underneath the printed circuit board, for example.
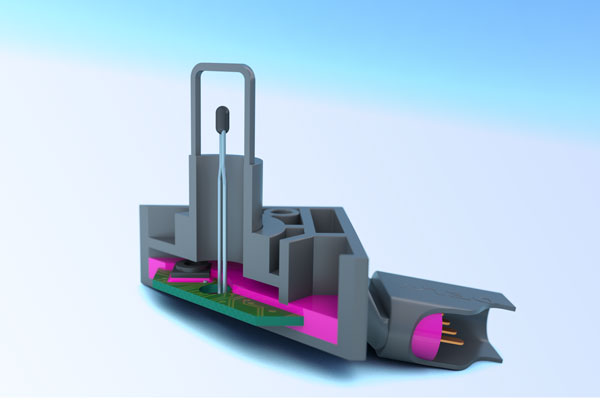
Adhesives and sealants for control units and plugs
Control units for motor or on-board electronics must be protected from humidity, media and corrosion, even under extreme temperatures. The most important task for adhesives and sealants is therefore the long-term protection of the control unit housing, plugs and other microswitches in the car. Another typical application is thermal management for power electronics. In air conditioning systems, for example, thermally conductive adhesives ensure that the heat generated under load is quickly dissipated to a heat sink.
Many DELO adhesives and sealants are developed specifically for these applications and for some of their special requirements, such as bonding to certain surface coatings. They provide the necessary reliability while enabling efficient production processes thanks to full curing or fixation within seconds and the enabling of in-line tightness testing.
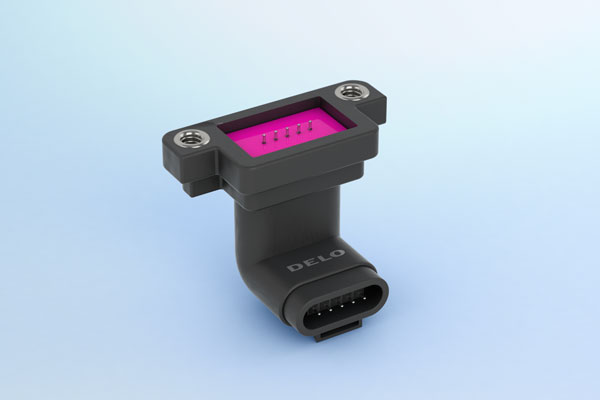
DELO products properties / strengths
- Very good sealing effect
- Good thermal cycling and media resistance
- Fast curing
- In-line tightness testing
Brochures for download
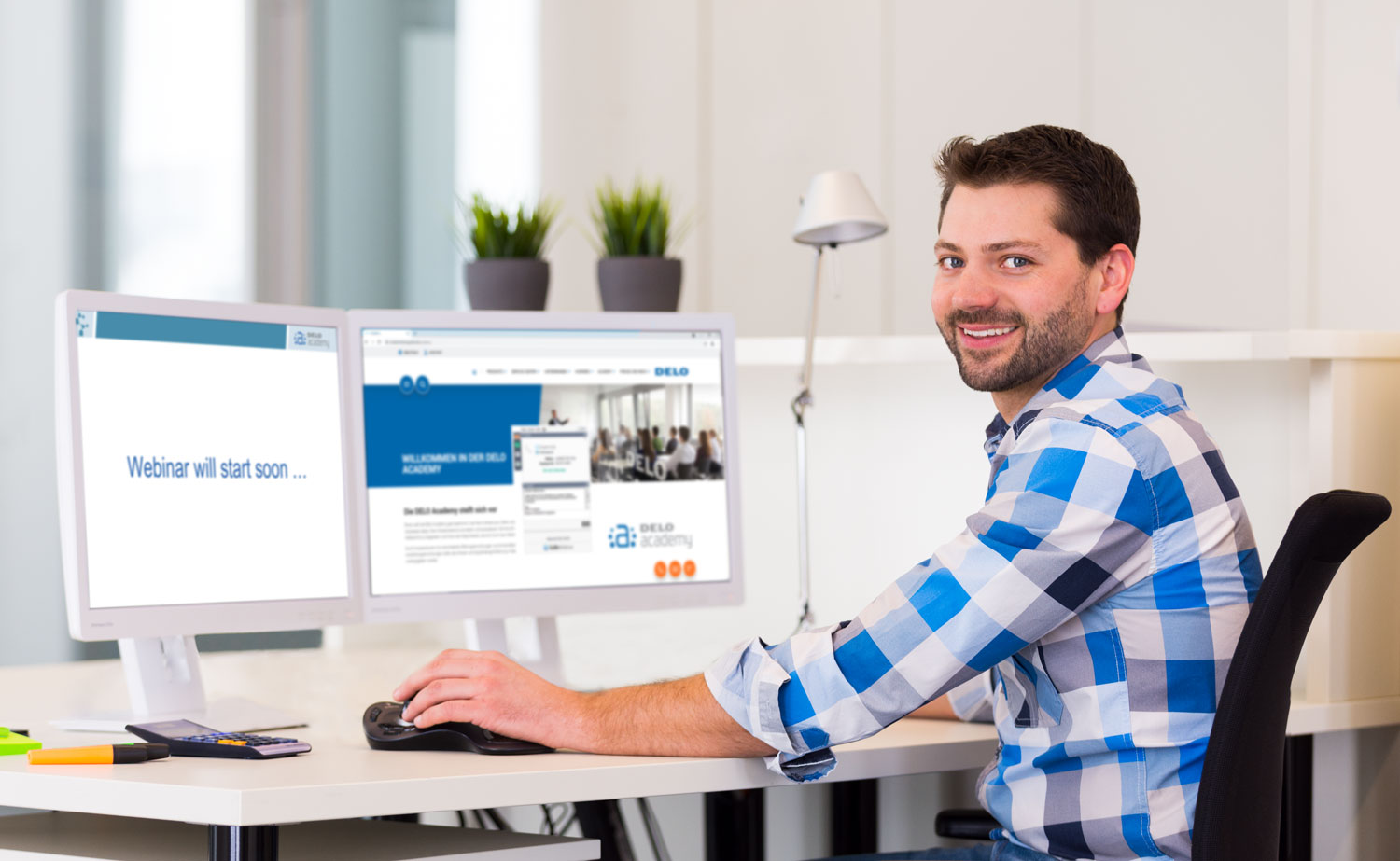
A digital knowledge package
Adhesive bonding is a demanding joining technology. To successfully solve bonding challenges, you need a good understanding of the basics and special features of this technology. Build up valuable knowledge with the help of our "TECH TALK" webinars!
Quick Request
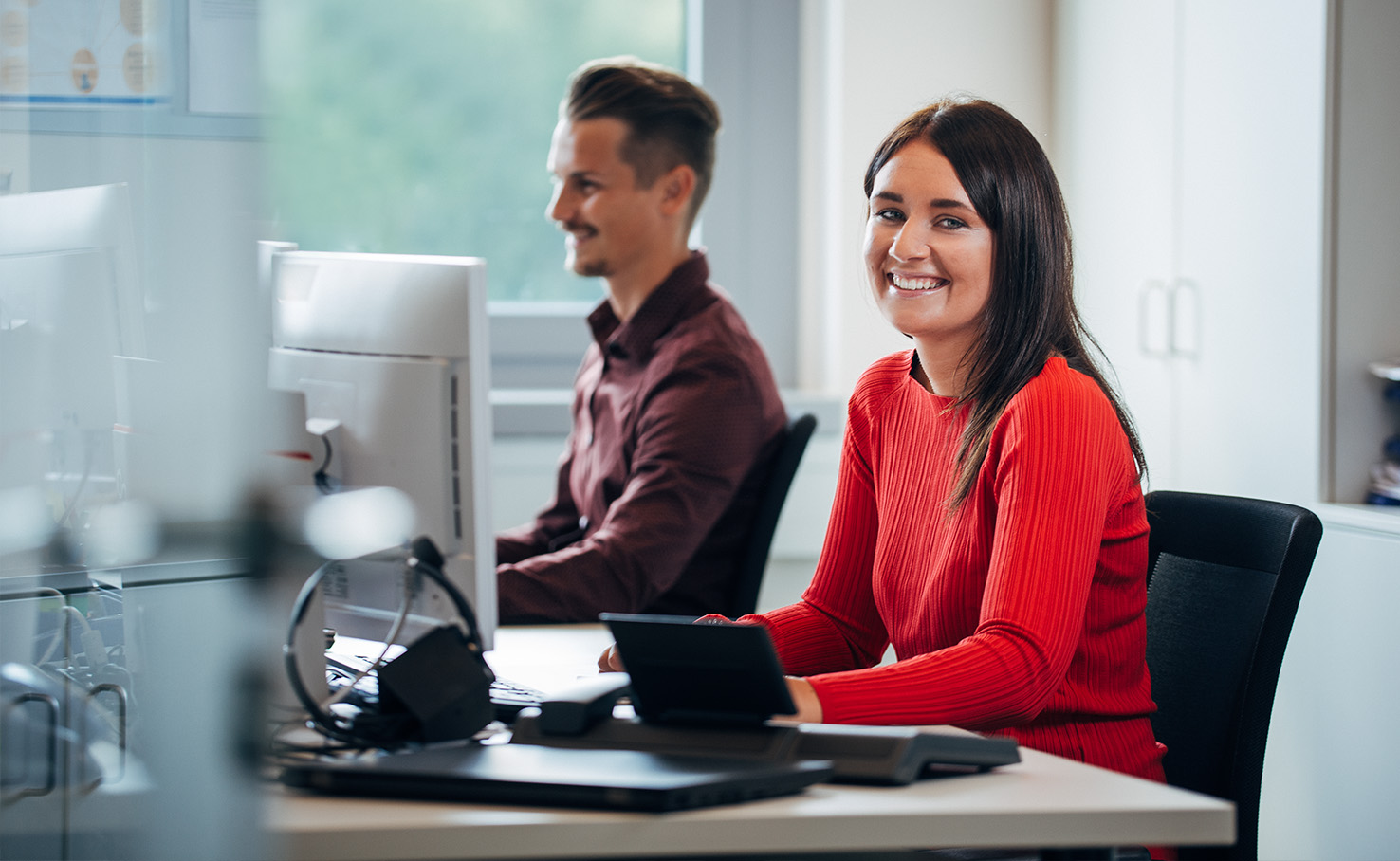
Do you have any questions?
Get in touch with us!
Technical consulting, sample and data sheet inquiries:
+49 8193 9900 - 9611
General & others:
+49 8193 9900 - 0