Curing processes
Adhesive curing – overview and comparison
Adhesives can be cured by light, heat, at room temperature, or in a dual curing process. With the optimum curing process, production times can be minimized and energy costs reduced significantly. The overview shows a comparison of common industrial curing methods and shows the advantages for the production process.
Light curing
Light- and UV-curing adhesives achieve full strength within seconds with the help of light. High-intensity LED curing lamps with wavelengths of 365 nm, 400 nm or 460 nm are used for the purpose. The key process parameters for full curing are irradiation time and intensity. And at least one component should be translucent for one of these wavelengths.
- Curing at room temperature within seconds
- Curing with light wavelengths of 365, 400 and 460 nm
- Particularly suitable for in-line production
- Low-energy curing process with LED lamps
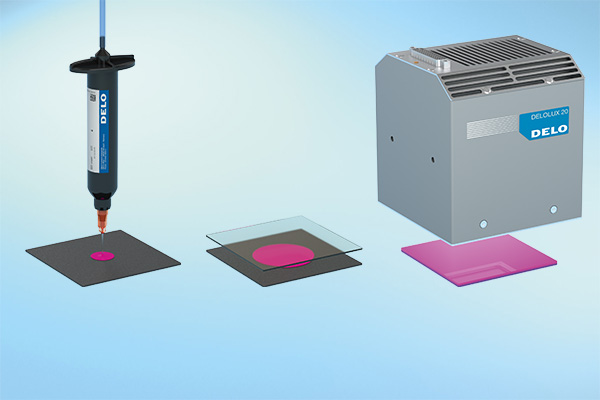
If both components to be bonded are opaque, light curing can still be used thanks to preactivation, thus omitting heat or the long waiting periods entailed in other room temperature curing methods. The process differs only slightly from that of light curing.
Dual curing
If fast light curing is to be used, but due to the geometry, shadowed areas are present in which the adhesive would not cure, dual-curing adhesives will ensure reliable curing. The first curing mechanism with light ensures fast fixation, while the second curing mechanism ensures full curing of the adhesive in the shadowed area.
Depending on the process, light curing can be combined with heat curing (from +60 °C) or humidity curing. Humidity curing is particularly interesting as a secondary curing mechanism as it utilizes the existing humidity in the air and thus enables production with a minimum carbon footprint. Room-temperature-curing products, such as two-component adhesives and anaerobic-curing metal adhesives are also available in the DELO portfolio as dual-curing adhesives.
- Good timing of adhesive curing for fast processes
- Fast fixation by means of UV and light curing
- Second curing mechanism for shadowed areas
- Heat or humidity curing depending on the components to be joined and the process
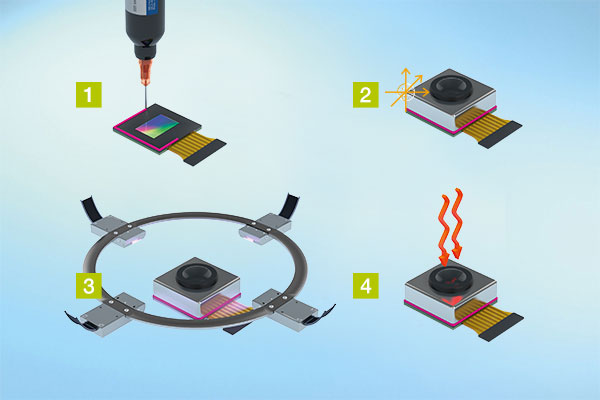
Heat curing
Heat curing is often used for structural adhesives, which are used as an alternative to traditional joining methods such as riveting or welding. Curing is performed at temperatures ranging from +60 °C to +180 °C. Air convection and tunnel ovens are generally used for the curing process. In some cases, induction can reduce the curing time 70-fold compared to convection ovens. Typical curing times are therefore between 60 seconds and 60 minutes. It is important to note that the temperature is applied to the adhesive and a possible heating time of the component must be taken into account.
- Particularly suitable for structural bonding
- In-line and batch processes possible
- For adhesives with maximum media and temperature resistance
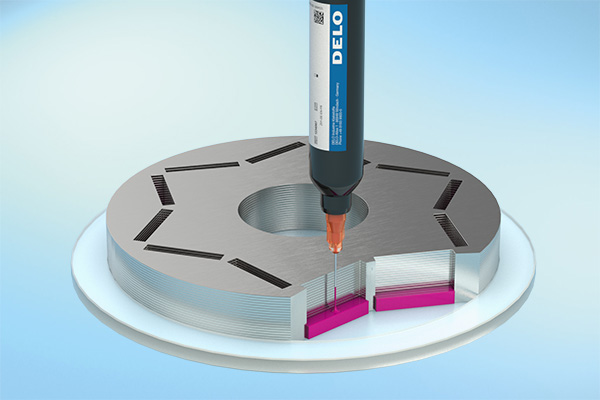
Room temperature curing
Two-component curing
Two-component adhesives cure at room temperature after mixing the resin and hardener (generally referred to as components A and B). No matter whether manually or fully automated, both components are dispensed via a mixing tube to ensure homogeneous mixing. Functional strength of the bonded components is often achieved after just a few minutes, with final strength generally being reached after 24 to 72 hours.
- Curing at room temperature with no further energy supply
- For manual and fully automated production
- Particularly suitable for small-volume production and large adhesive quantities
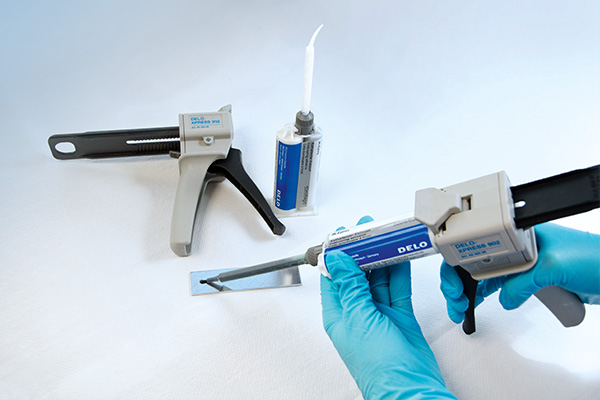
Anaerobic curing
Anaerobic-curing adhesives, colloquially referred to as metal adhesives, or more commonly as screw locks, cure under the absence of oxygen and through contact with metal ions on the metal surface. After curing for just a few minutes, the components to be bonded can continue to be further processed. The process speed can be increased by additional light fixation or the use of activators or primers.
- Curing process with the lowest energy input
- Particularly suitable for batch production
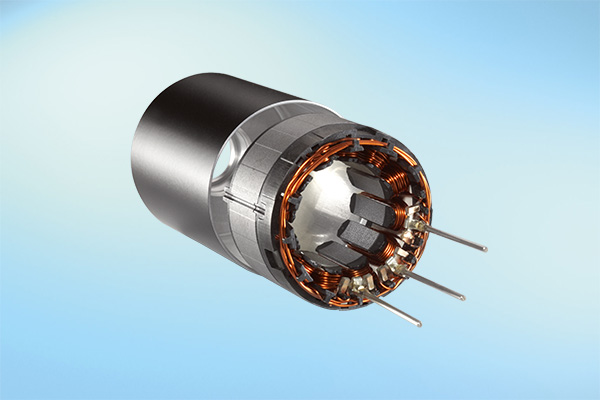
Curing with humidity
The best-known adhesives that cure with air humidity are without doubt silicones and superglues (cyanoacrylates). In fast, fully automated processes however, dual-curing adhesives are mainly used. They are first of all prefixed with light and then, in a second step, cured with the humidity in the air. The speed of the second step depends on the component geometry and the degree of relative humidity, but is usually completed within 72 hours.
Brochures for download
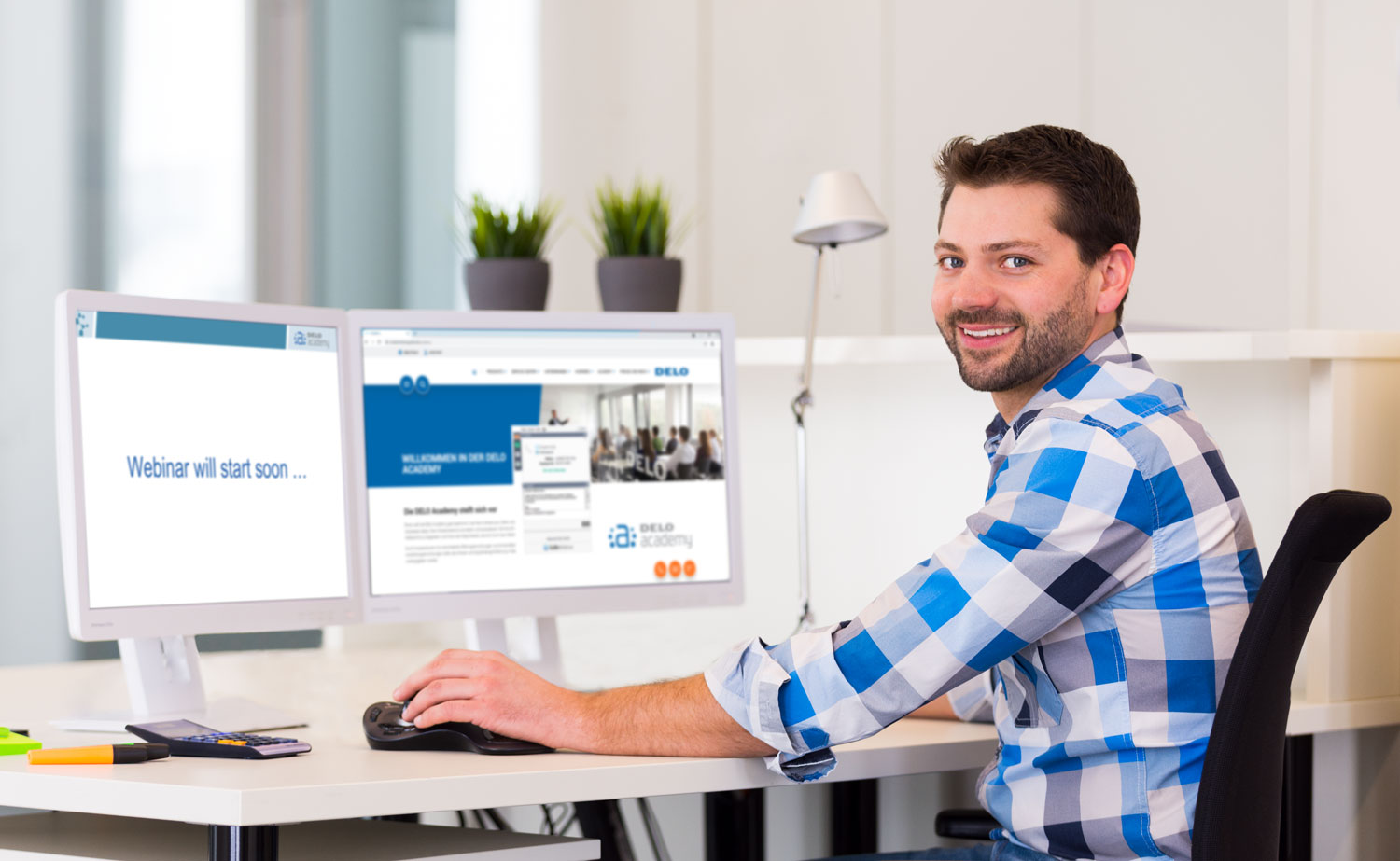
A digital knowledge package
Adhesive bonding is a demanding joining technology. To successfully solve bonding challenges, you need a good understanding of the basics and special features of this technology. Build up valuable knowledge with the help of our "TECH TALK" webinars!
Quick Request
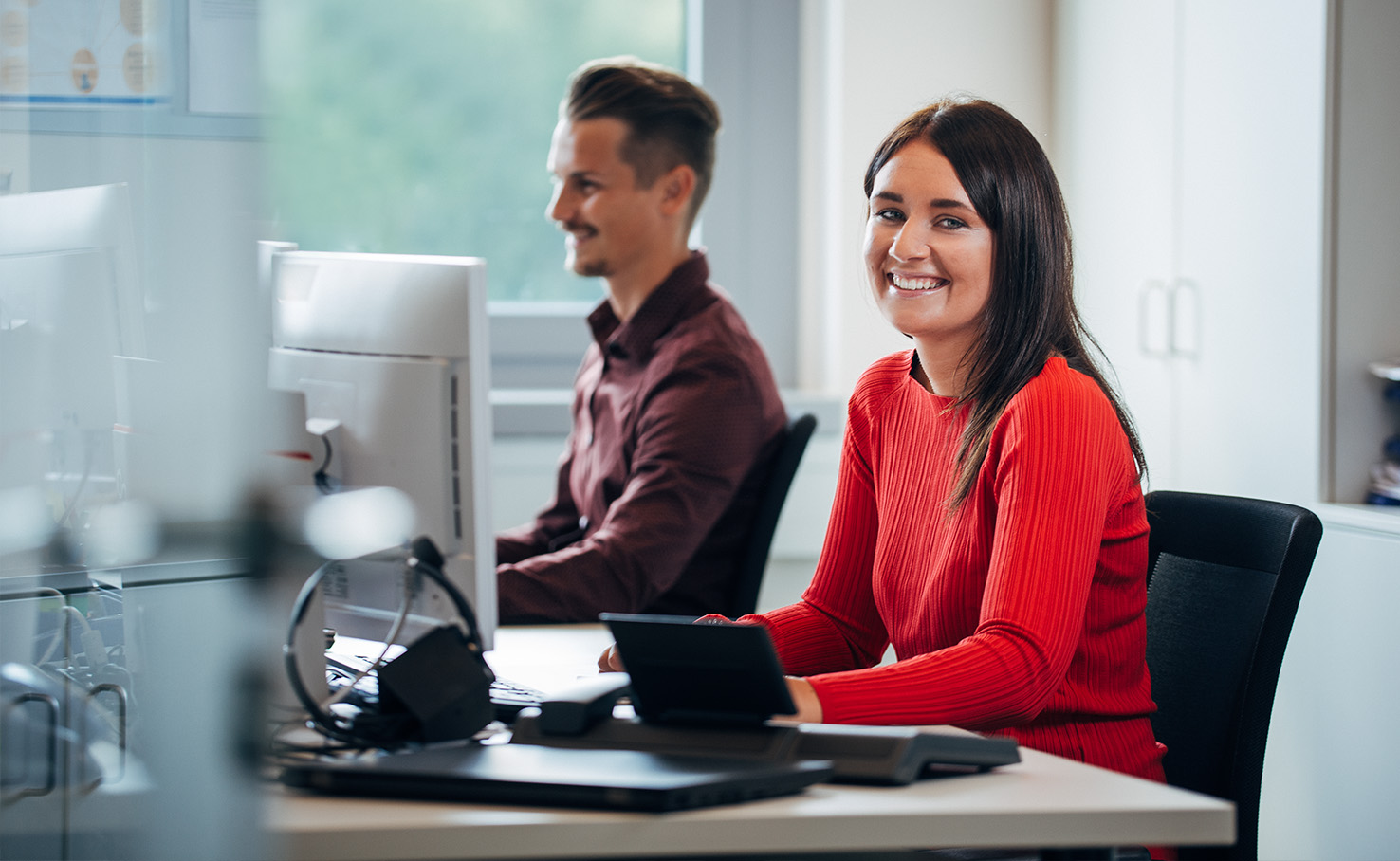
Do you have any questions?
Get in touch with us!
Technical consulting, sample and data sheet inquiries:
+49 8193 9900 - 9611
General & others:
+49 8193 9900 - 0